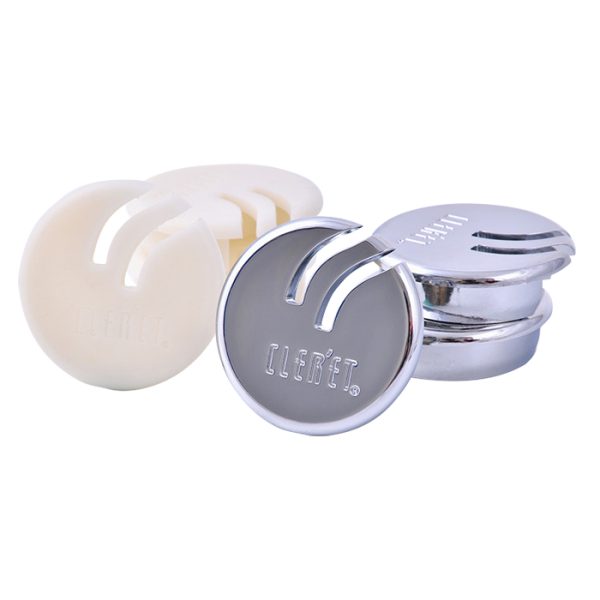
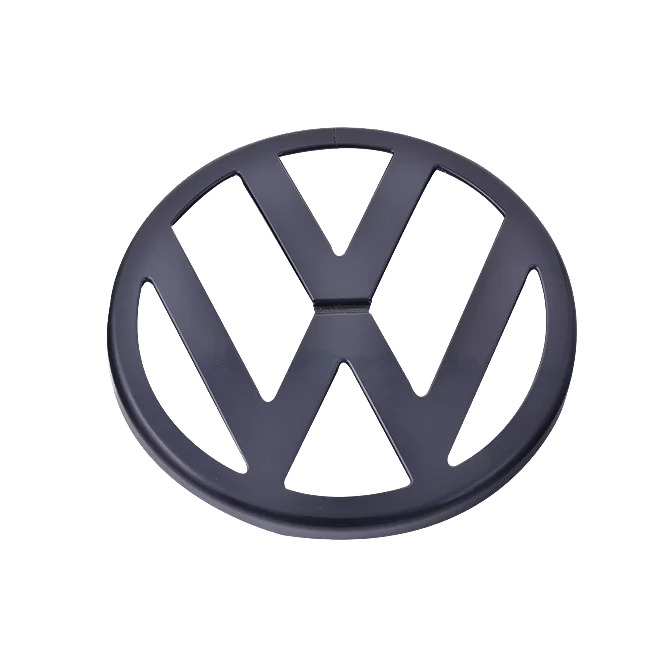
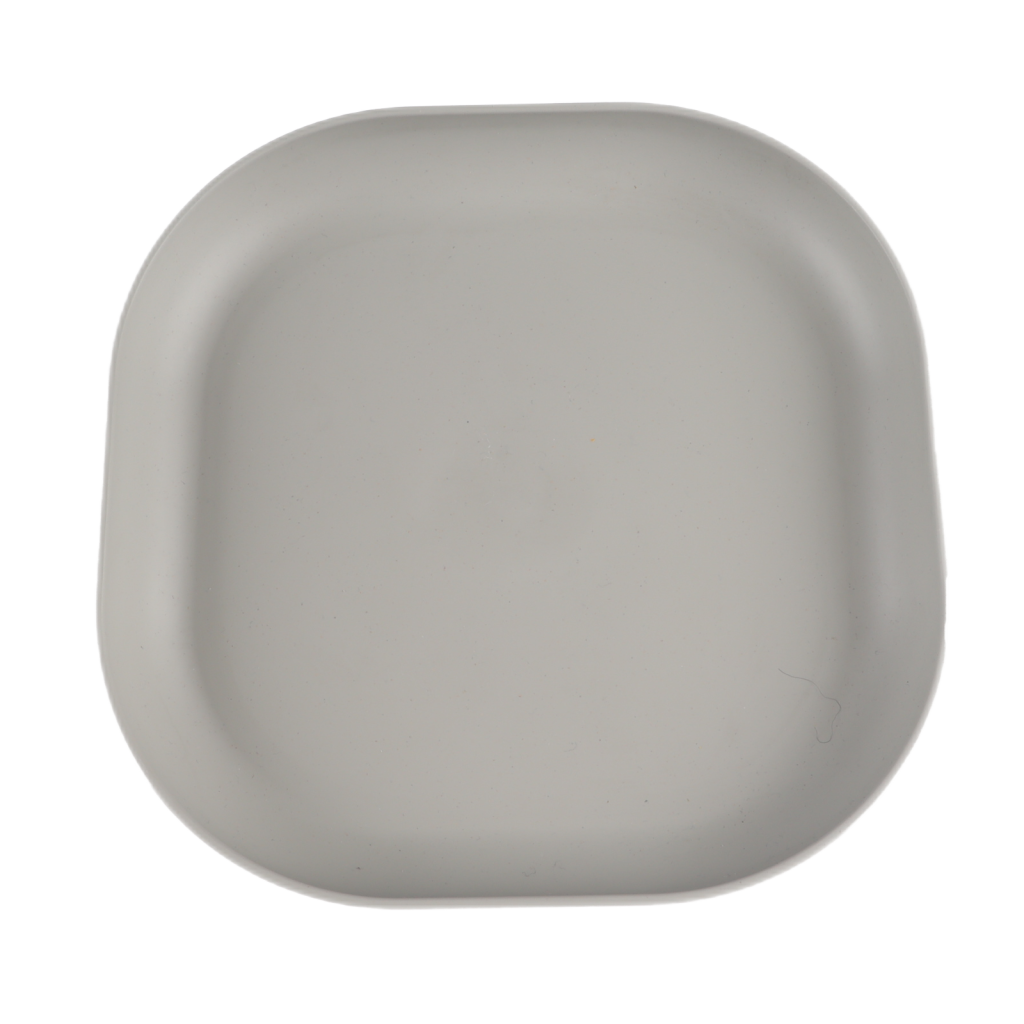
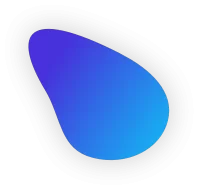
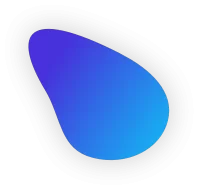
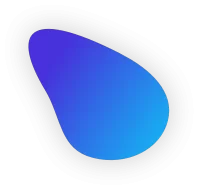
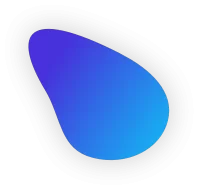
What is the Injection Molding?
Injection molding is an elegant and simple manufacturing process that can quickly produce intricate shapes for custom parts and products. Injection molding is the process of choice for companies looking to produce repeatable parts with strict mechanical requirements.Injection molding is a popular manufacturing option for high-production runs, not only because of the consistent quality of the manufactured plastic parts, but also because the price-per-part decreases with higher quantity manufacturing runs.
The advantages
- Rapid prototype producing
- High-accuracy and small tolerance
- Stable processing quality
- Cost effective and efficient when small and medium-volume runs
How Injection Molding works?
Injection molding is the use of plastic thermal physical properties, the material from the hopper into the barrel, the type of barrel by the heating ring heating, so that the material melting, in the barrel is equipped with external power motor under the action of driving rotation of the screw, material under the action of the screw;
Transport along the spiral groove and compaction, material in plus heat and screw shear gradually under the dual role of plasticizing, melting and homogenization, when screw rotation, the material in the screw groove under the action of friction force and shear force, pushing has molten material to the screw head, at the same time, screw back under the adverse effect of material, make the screw head form the loading space, complete the plasticizing process;
Then screw in the injection cylinder piston under the action of thrust, with high speed, high pressure, the store is indoor material melt through the nozzle of the injection into the mold cavity, the cavity of the molten material after pressure maintaining and cooling, curing finalize the design, mold under the effect of clamping mechanism, open mold, and by the ejection device and by ejection device to finalize the design good products sets out from the mold.
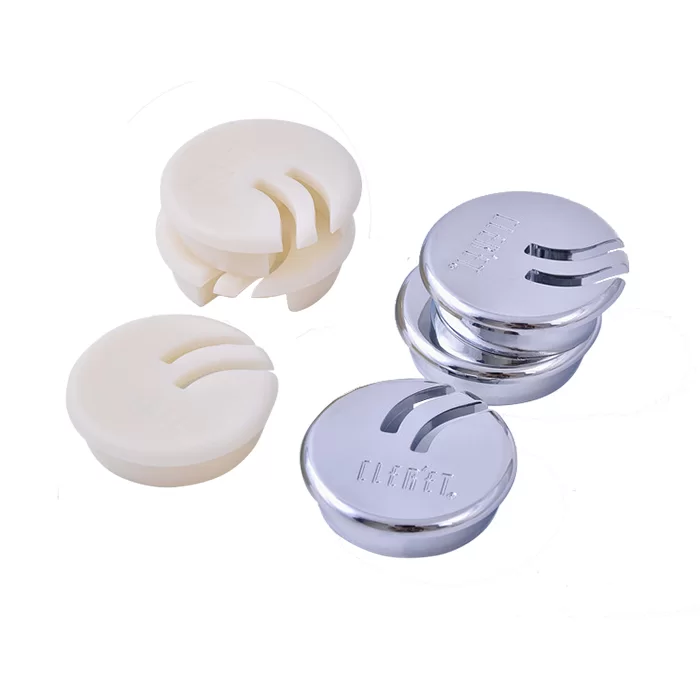
Features of Injection Molding
Injection molding is a method of molding industrial products. Products usually use rubber injection molding and plastic injection molding. Injection molding can also be divided into injection molding, molding and die-casting.
Injection molding machine (hereinafter referred to as injection machine or injection molding machine) is the main molding equipment that uses plastic molding molds to make thermoplastic or thermosetting materials into plastic products of various shapes. Injection molding is realized through injection molding machines and molds.
Advantages
Drawbacks
Materials for Injection Molding
Hard Plastics | Flexible Plastics | Rubber-Like Varieties | Mixed plastic |
---|---|---|---|
ABS | Acrylonitrile Butadiene Styrene | Polyethylene ( PE ) | TPE | Thermoplastic Elastomer, Santoprene | PC-ABS | Polycarbonate-Acrylonitrile Butadiene Styrene |
ASA | Acrylonitrile Styrene Acrylate | Polystyrene ( PS ) | TPU | Thermoplastic Polyurethane ( Shore A) | PC-PBT | Polycarbonate-PolybutyleneTerephthalate |
CA | Cellulose Acetate | PET | LSR | Liquid Silicone Rubber | PC-PET | Polycarbonate-Polyethylene Terephthalate |
COPO | Copolyester | EVA Foam | LSR | Liquid Silicone Rubber | PS-PPE | Polystyrene-Polyphenyl Ethers |
PCT I Polycyclohexylenedimethylene Terephthalate | EPS Foam | PVC | Polyvinyl Chloride ( Shore A) | PE-PS | Polyethylene-Polystyrene |
PPA | Polyphthalamide | PU Foam | POE | Polyolefin Elastomer | PE-PP | Polyethylene-Polypropylene |
HDPE | High-Density Polyethylene | MPR | Melt Processable Rubber | PBT-PET | Polybutylene Terephthalate -Polyethylene Terephthalate | |
PEEK | EPDM | Ethylene Propylene Diene Monomer Rubber, Viton | PBT-PET | Polybutylene Terephthalate -Polyethylene Terephthalate | |
Polypropylene ( PP ) | |||
Polycarbonate ( PC ) | |||
PMMA I Polymethyl Methacrylate , Acrylic | |||
Nylon 12 ( PA12 ) | |||
Nylon 6 / 66 ( PA6 / 66 ) | |||
Derlin ( POM) | |||
Teflon ( PTFE ) | |||
PBT | |||
PLA I Polylactic Acid | |||
High-Density Polyethylene ( HDPE ) | |||
PVC | |||
PPS | Polyphenylene Sulfide , Ryton | |||
Vespel ( PI ) | |||
Torlon 4203 ( PAI) | |||
UPE / UHMW | |||
PVDF | |||
ULTEM ( PEI) |
Surface Finishes for Injection Molding
Printing | Painting |
---|---|
Screen screen printing | Ordinary coloring |
Curved surface printing | Pu gloss |
Bronzing |