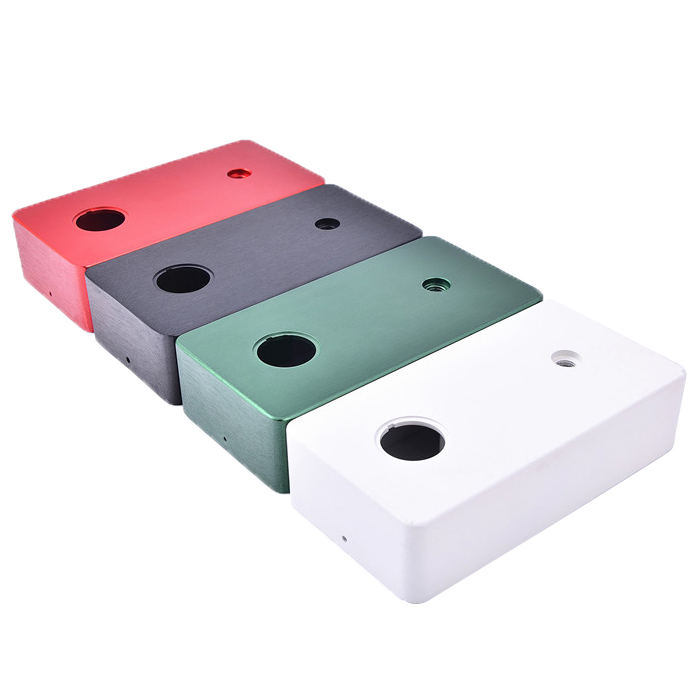
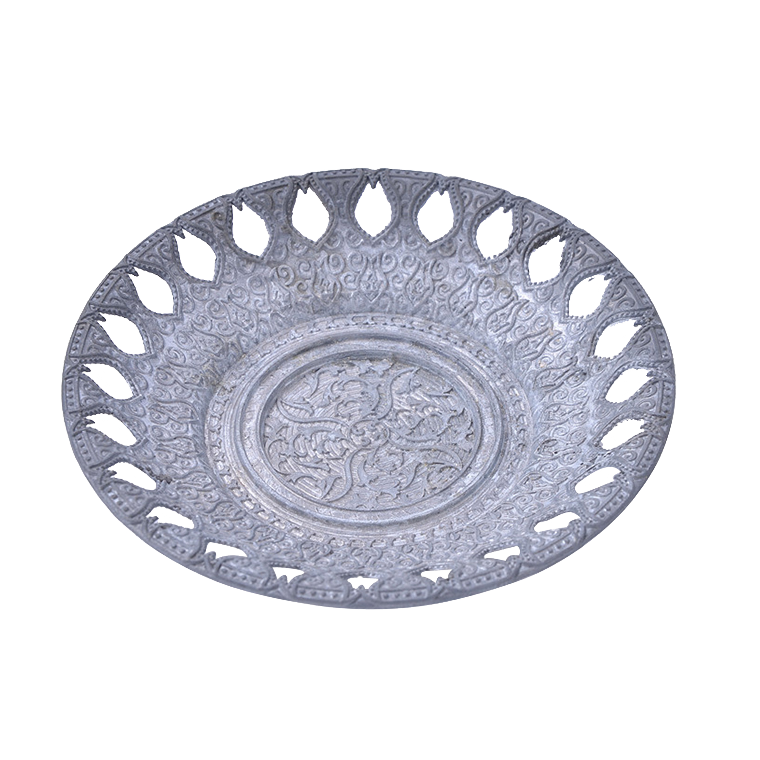
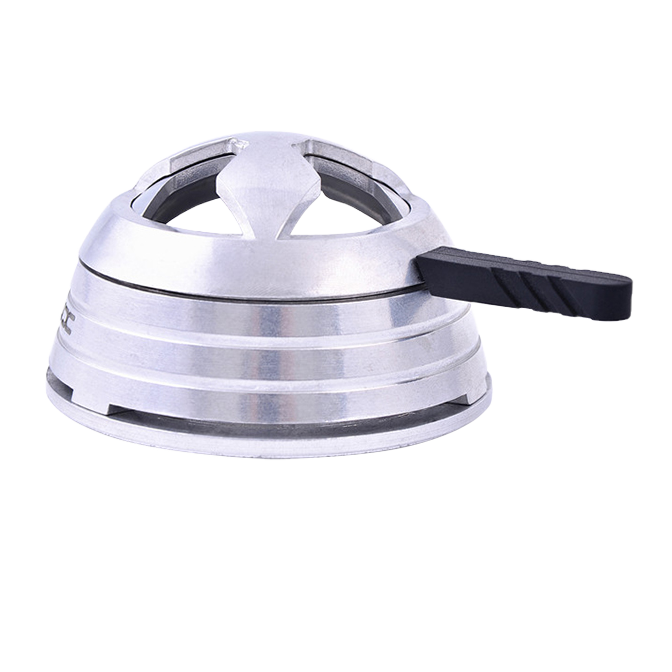
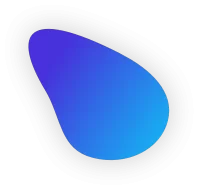
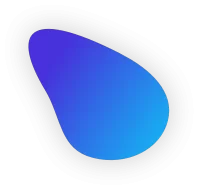
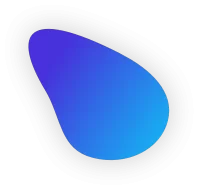
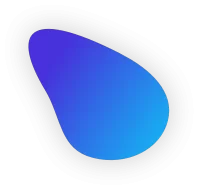
What is the Die Casting?
Die casting is a manufacturing process that produces metal parts using molds (also called dies). It involves forcing molten metal into a mold cavity (under high pressures) to create the desired metal parts.The mold consists of two halves (usually made of heat-resistant steel grades) that form a cavity into which the liquid metal is pressed at pressures ranging from 1,000 to 20,000 psi. The die casting process comes in two typesㅡwhich are hot chamber and cold chamber die casting processes.
The advantages
- Rapid prototype producing
- High-accuracy and small tolerance
- Stable processing quality
- Cost effective and efficient when small and medium-volume runs
How Die Casting works?
Die casting uses high pressure to push liquid metal into a precision metal mold cavity at high speed, “almost the same as plastic”. Metal die casting is the metal liquid under pressure under the action of cooling solidification and forming castings. Cold chamber die casting and hot chamber die casting are two basic methods of die casting process. In cold chamber die casting, liquid metal is poured into the pressure chamber by manual or automatic pouring device, and then the injection punch is advanced, and the metal is hydraulically injected into the model chamber. In the hot chamber die casting process, the chamber is perpendicular to the crucible, and the metal liquid flows into the chamber automatically through the feed port on the chamber. The injection punch moves downward to push the metal liquid through the gooseneck into the cavity. After the metal solidifies, the product is formed, the die casting mold is opened, the casting is removed, and a die casting cycle is completed.
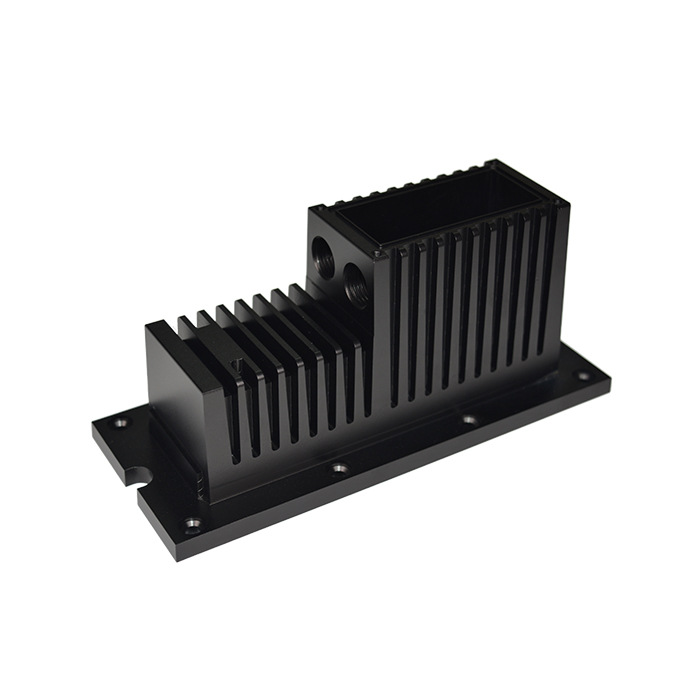
Features of Die Casting
Advantages
The advantages of die casting include excellent dimensional accuracy. The error is 0.02CM, the casting surface is smooth, and the fillet radius is about 1-2.5 microns. It can directly cast the internal structure. Reduce or avoid secondary machining, fast production speed, casting tensile strength up to 415 MPa, can cast high liquidity metal.
Drawbacks
Mold and mold related components are very expensive for it. This process is only applicable to metals with high fluidity, and the casting quality must be between 30g and 10kg. There will be pores, so no heat treatment or welding can be carried out.
Materials for Die Casting
aluminum die casting | Zinc die casting |
---|---|
A356.0 | ZA-2 |
A360.0 | ZA-3 |
A380.0 | |
A383.0 (ADC12) | |
A413.0 |
Surface Finishes for Die Casting
surface finishes | ||
---|---|---|
Anodizing | Bright Nickel | Silver |
Chromate | Chem Film | Nickel-Free Coating |
E-Coat | Copper-nickel-tin | Polyurethane paint |
Black Oxide | Cobalt tin | Impregnation |
Powder Coat | Electroless nickel | Teflon |
Chrome Plated | Gold plating |