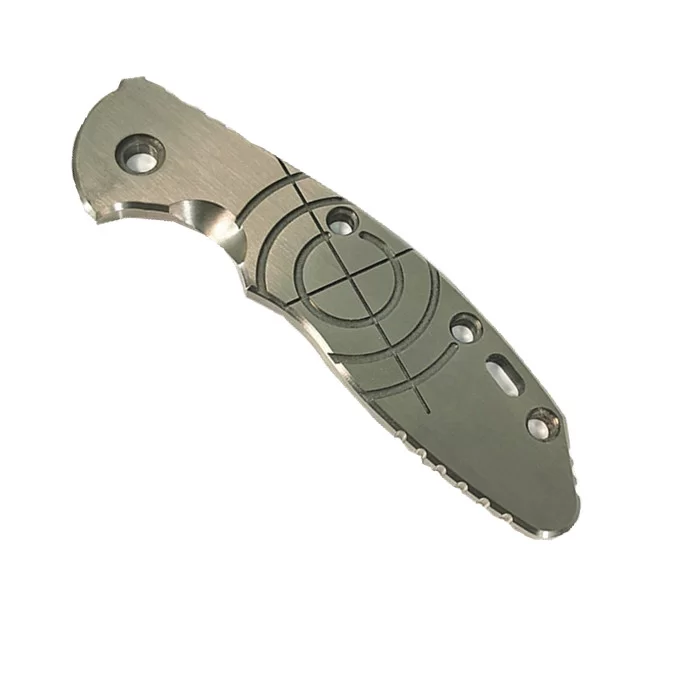
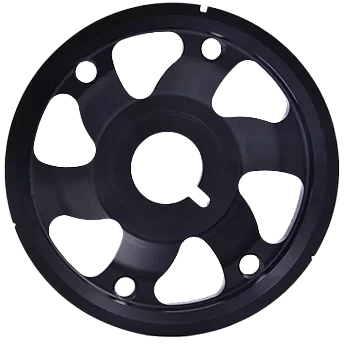
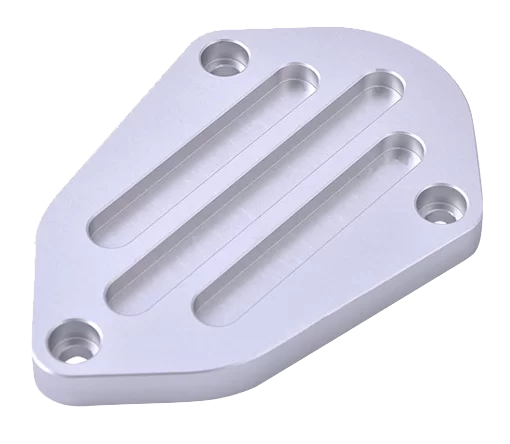
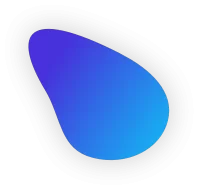
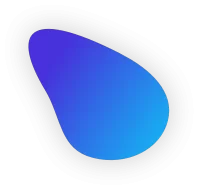
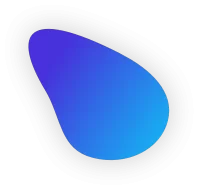
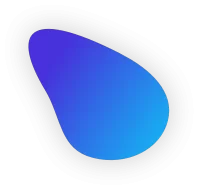
What is the CNC milling?
CNC milling is based on the shape, size tolerance, surface roughness of the part and other technical requirements to create program and select processing parameters, then through CNC machining language programming and control tool feed speed and spindle speed, as well as tool converter coolant to achieve the workpiece milling to finish the parts manufacturing
The advantages
- Rapid prototype producing
- High-accuracy and small tolerance
- Stable processing quality
- Cost effective and efficient when small and medium-volume runs
How CNC Milling works?
CNC milling machine processing in fact the application of the “differential” principle, its working principle and process is described as follows.
1) According to the tool path required by the processing program, the NUMERICAL control device differentiates the path according to the corresponding coordinate axis of the machine tool with the minimum movement (pulse equivalent) as the unit, and calculates the number of pulses that need to move in each coordinate.
2) Through the “interpolation” software or “interpolation” arithmetic unit of the NUMERICAL control device, the required trajectory is fitted with the equivalent broken line as the unit of “minimum movement”, and the fitted broken line closest to the theoretical trajectory is found.
3) According to the trajectory of the fitted broken line, the NUMERICAL control device continuously allocates the corresponding coordinate axis to the feed pulse, and makes the coordinate axis of the machine tool move according to the assigned pulse through the servo drive.
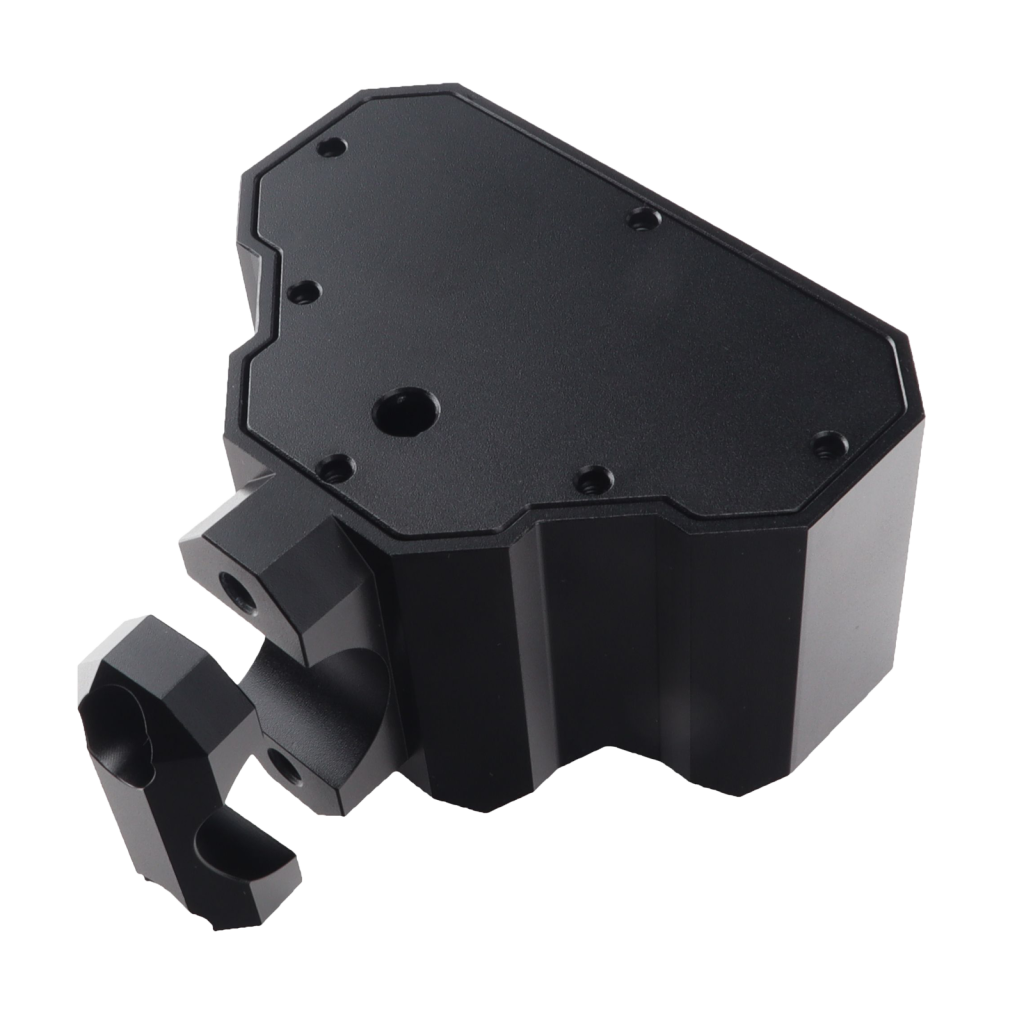
Features of CNC Milling
Milling refers to the use of rotating multi edge tools to cut the workpiece, which is an efficient processing method. It is suitable for machining planes, grooves, various forming surfaces (such as splines, gears and threads) and special surfaces of molds.
Advantages
Drawbacks
1. More friction, blunt blade and short service life.
4. It consumes a lot of energy.
Materials for CNC Milling
Aluminum | Steel | Copper / Brass / Titanium / Zinc | Plastics | Others |
---|---|---|---|---|
2A12 | 201 | Copper | ABS | Bakelite |
5052 | 303 | Brass | Transparent ABS | Rubber |
7075 | 304 | Titanium(Ti) | Polycarbonate (PC) | FR4 |
6061 | 316 | Zinc(Zn) | Acrylic (PMMA) | Others |
others | 430 | Mild steel(Low Carbon Steel) | Delrin/Acetal (POM) | - |
- | - | Alloy steel | Polyethylene (PE) | - |
- | - | Tool steel | PTFE (Teflon) | - |
- | - | - | PEEK | - |
Surface Finishes for CNC Milling
As-Milled
Requirement
none
Grit
none
Thickness
none
Surface roughness
none
Color
none
Part masking
none
Bead Blast
Requirement
Specification
Grit
#120
Thickness
none
Surface roughness
none
Color
Uniform matte of raw material color
Part masking
Indicate masking requirements in technical drawing
Anodized(Type II Or Type III)
Requirement
Specification
Grit
#120
Thickness
none
Surface roughness
none
Color
Uniform matte of raw material color
Part masking
Indicate masking requirements in technical drawing
Bead Blasting + Anodizing color or clear(type II)
Requirement
Specification
Grit
none
Thickness
8 - 12 μm (clear), 4 - 8 μm (color)
Surface roughness
none
Color
Black, clear or any RAL code or Pantone number
Part masking
Indicate masking requirements in technical drawing
Powder Coat
Requirement
Specification
Grit
none
Thickness
18 - 72 μm
Surface roughness
none
Color
Black or any RAL code or Pantone number
Part masking
Indicate masking requirements in technical drawing
Electropolished
Requirement
Specification
Grit
none
Thickness
none
Surface roughness
none
Color
Natural metal color
Part masking
Indicate masking requirements in technical drawing
Brushed
Requirement
Specification
Grit
#80-120
Thickness
none
Surface roughness
0.8 - 1.5 μm
Color
none
Part masking
Indicate masking requirements in technical drawing